ENGINEERING SERVICES
PARCS Ltd. has an in-house team of professional engineers with extensive expertise in design, safety, structural analysis and regulatory compliance.
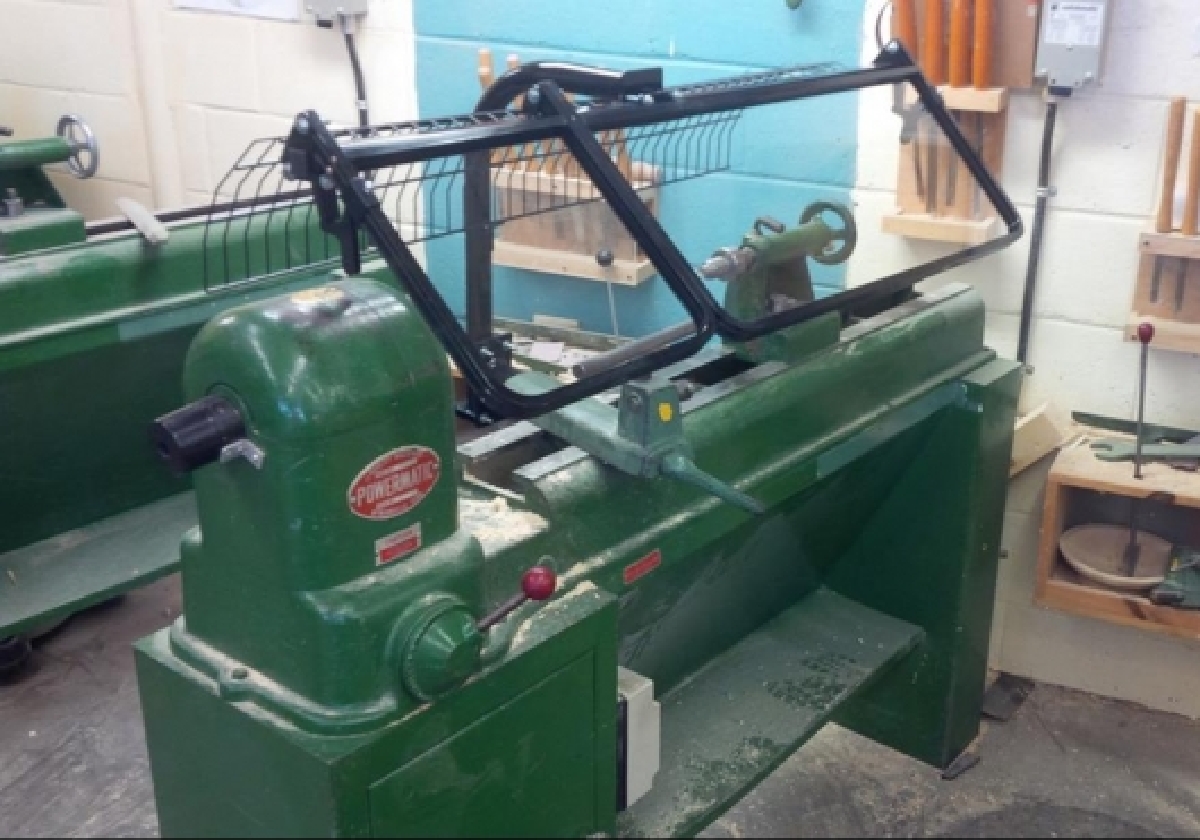
Shop Equipment
Shop equipment assessments are often required/performed in woodworking, machine, automotive, and combined machinery shops.
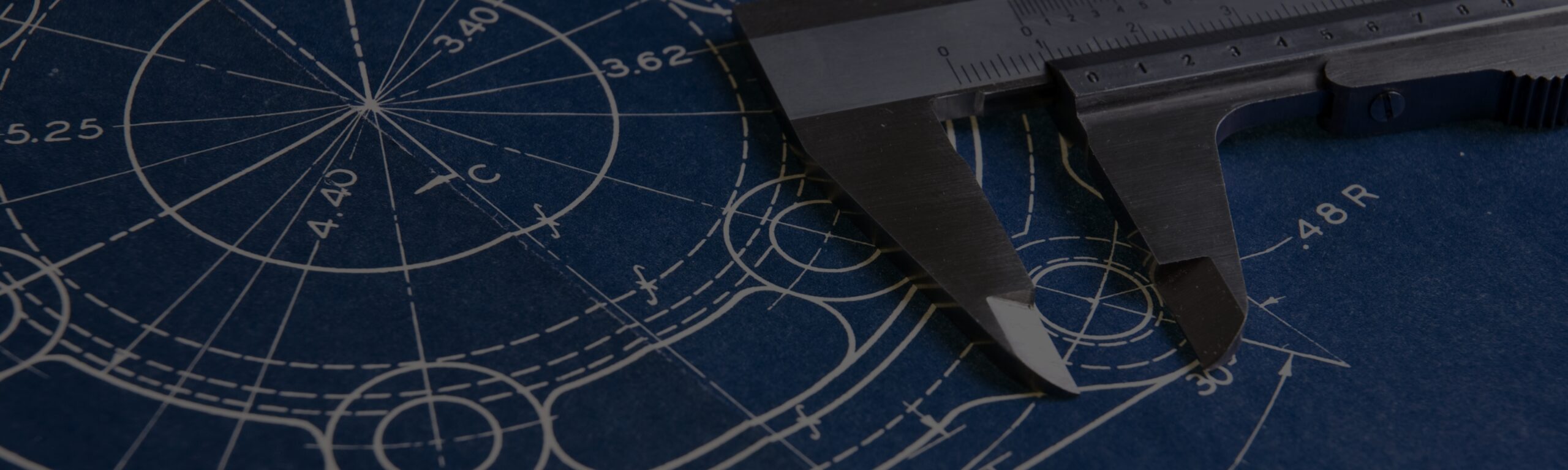
PSHSR – Pre-start health and safety reviews
A Pre-Start Health and Safety Review is an assessment by a Professional Engineer of any Industrial apparatus, protective element, process, or structure, to ensure compliance with applicable standards.
Products
Custom Engineering
Concept
Taking a collaborative approach, we work with our clients to investigate all of the requirements of a project from a productive, environmental, usage and safety capacity. Then we use this information to inform our in-house design team.
Design
Our in-house design team combines their years of collective experience in manufacturing design and engineering with technical software and regulatory knowledge to design a solution for the project at hand to be sent for approval from our in-house engineering team.
Approval
Our in-house engineering team makes adjustments to make sure the initial design meets or exceeds all capacity, usage, environmental, safety and regulatory criteria and approves the project for fabrication.
Fabrication
Our team of CWB Certified welders brings the approved design concepts created by our design and engineering teams to life in our 30,000 sq ft fabrication facility.
Inspection
Once a project has completed the fabrication stage, it is inspected and tested to ensure all capacity, usage, environmental, safety and regulatory criteria are met or exceeded.
Installation
Once final inspection is completed, your project is ready for the installation phase, which includes physical installation, implementation of in-site training, adjustments (as needed), a Prestart Health and Safety Review, exemption letters, engineering sign-offs, and electrification according to CSA C22 standards (if applicable).
Your Perfect Solution Awaits!
Engineering and Design Consultations
We meet all your custom product needs from start to finish. Our in-house engineering team will ensure quick sign-off on all custom orders and testing while meeting the exact specifications required for your facility.
You can expect top-of-the-line products and excellent customer service. From design to implementation, our team will walk you through the process and help you reach the best solution for your facility needs.
To request a consultation, please fill out the form attached to this page and we will reach out to book a consultation that fits into your schedule. You can also contact us directly at:
3 Steps To Fall Protection Compliance
1. EVALUATE YOUR FALL PROTECTION NEEDS:
- Plan ahead to get the job done safely.
- Assess areas on your rooftop that require access.
2. ASSESS THE RISKS:
- Are my employees or contractors at risk of a fall?
- Am I exposing my company to unnecessary fines?
3. IMPLEMENT A SOLUTION:
- Provide the right fall protection equipment.
When is fall protection required?
Most jurisdictions require the use of specific fall protection measures before, or in addition to, personal protective equipment (PPE). These measures generally include the use of some of the following:
fixed barriers (e.g., handrails, guardrails)
surface opening protection (e.g., covers, guardrails, etc.)
warning barriers/control zones
fall or travel restraint systems (i.e., a system to prevent a worker from falling from a work position, or from travelling to an unguarded edge from which the worker could fall)
fall containment system (e.g., safety nets)
fall arrest systems (i.e., a system that will stop a worker’s fall before the worker hits the surface below)
There may also be specific legal requirements around use of equipment like ladders and scaffolding.
Occupational health and safety laws generally require action when a worker has the potential to fall about 3 metres (10 feet). In most cases, fall protection is required when:
other means of fall protection are not available or possible, such as guardrails
working at a height of 3 metres or more (permanent and/or temporary work areas)
working at a height of less than 3 metres when the surface below could cause a greater injury than just the fall (e.g., machinery; risk of drowning in water or other liquid; open tanks, vats, or pits containing hazardous materials; materials that can shift)
a worker may fall through an opening in the work surface
it is determined that fall protection is necessary
https://www.ccohs.ca/oshanswers/hsprograms/fall%20protection_legislation.html
What our clients are saying
We really appreciated your quick response and time to address this concern. Thank you also for being proactive and getting a quote for repairs.
Lastly, I wanted to let you know that I was very happy to hear from our custodians that your staff who were performing some hot work this past summer were following all the required legislated requirements for this type of work. We implemented our program this fall and during training they told me how you had a fire watch, a permit and your own extinguisher. Way to go!
Over the years we have worked with a number of various companies for inspections and repairs of our equipment. Having to locate reports is cumbersome, time consuming and not cost effective.
Having G10 keep all of our reports, certificates, maintenance forms and documentation in one location is exactly what we needed. The computer generated certificates and ability to approve quotes online really exceeded our expectations. Great work!
We are very glad that your crew recognized that the incorrect anchors were supplied and made the switch to the proper ones. The technicians were prompt, knowledgeable, and friendly.
Thanks again, for organizing the repair so promptly. The whole process was quick and I am so happy we can open the playground on Tuesday for the kids.
We have been exceptionally happy with the professionalism of the company and the customer service they provide. Whatever the insepction, PARCS provides detailed reports outlining the findings. These have been well received by use, the Health and Safety departement, as well as the school administrators and teachers.
If ever we have a concern or question, it is responded to almost immediately. It is with pleasure that we recommend the services of PARCS Ltd. to other organizations.
About PARCS Inc.
Learn more about our team and what sets us apart as industry experts in certified safety inspections, repairs, installations and engineering for playgrounds, gymnasiums, auto and woodworking shops.
Resource Center
Learn from the experts about all things safety within your industry. Browse our Resource Center to find case studies, articles, product catalogues and more.
Customer Service
Request a quote
Have questions?
Give us a call. Our friendly customer service staff are on hand and ready to help you.